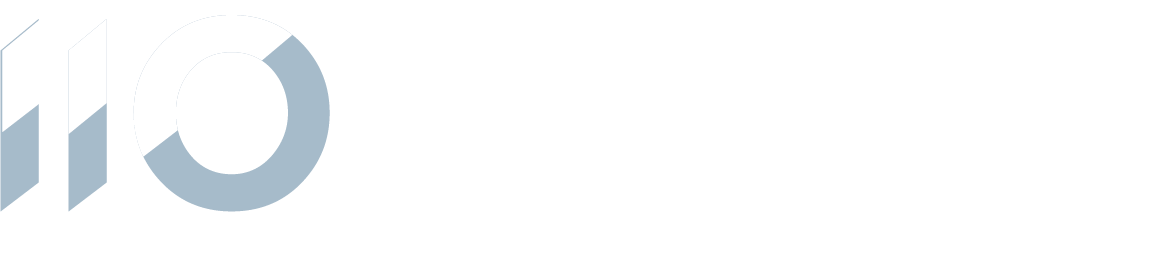
Taking control of combustible cladding
The tragic fire at Grenfell Tower in London in 2017 initiated a global movement to address the risk of combustible cladding on buildings. While governments in Australia have implemented a raft of measures, many strata communities lack the confidence to remediate their building.
‘Where should I start? How can I control cost? Who should do the work?’
Paynter Dixon’s team of remedial experts work closely with strata managers, building owners and owners corporations to create compliant solutions for impacted buildings. Here are a number of key considerations.
The risk of waiting
Delaying the job raises the stakes. The ABC has previously reported building insurance premiums rising by as much as a multiple of four.
The cost of insuring impacted buildings in Canberra has also gone through the roof, with many premiums increasing by 30 to 100 per cent during the past 12 months.
The ‘limitation on liability’ in policies is also seeing a reduction to the covered losses insurers are willing to pay.
Government fast facts
Register building
NSW Government amended legislation in 2018, creating a requirement for owners of certain buildings with combustible cladding to register their building through an online registration system.
Assessing the risk
The NSW Cladding Taskforce was also established to assess the fire risk of buildings. Consent authorities – including local councils and the Department of Planning and Environment – have performed assessments.
Funding the remediation
Project Remediate is a voluntary opt-in program for eligible class 2 residential apartment buildings, offering 10-year interest-free loans to support the re-cladding process. Registrations are closing on 16 December 2022.
Flammable on multiple fronts
Aluminium Composite Panels (ACP) typically consist of a polyethylene core sandwiched between two thin sheets of aluminium. Expanded Polystyrene Systems (EPS) consist of bulk foam insulation fixed to a structural frame and then sealed, rendered, and painted.
ACPs and EPS systems are both highly flammable – approaching petroleum. It’s not just the materials that determine flammability. Building design and other materials can exacerbate a fire as well.
Which cladding products are compliant?
The Deemed-to-Satisfy Provisions of the National Construction Code (C1.9) require the external walls and other specified components of certain buildings to be ‘non-combustible’. A product can be regarded as ‘non-combustible’ if it has been tested to and met the
relevant criteria in AS 1530.1.
Where can you see the current status of products? The Cladding Product Safety Panel is an advisory committee to the NSW Cladding Taskforce and has published a consolidated list of cladding materials on its website.
Early Contractor Involvement
Cladding can hide a multitude of building issues. It is why we recommend working up front with the contractor, referred to as Early Contractor Involvement (ECI). This is a proven method of managing risk and cost from the outset, guided by our 5 stage process. It can also present opportunities for recycling used building materials.
Our 5 stage process
- Risk profiling
A visual assessment of the building and gauging risk factors in re-cladding. - Detailed investigation
The involves peeling back a section of the building skin to assess underlying materials and potential sub-structure issues. This avoids nasty – and costly – surprises later in construction. - Planning
This seamless ‘back of house’ coordination spans design and documentation, compliance, cost planning and contractor engagement. - Authority approvals
This can include lodging a Development Application, Complying Development Certificate, or meeting the requirements of a Fire Order. - Construction
Our site team manages work on site with minimal disruption to building occupants. Accreditation with the Federal Safety Commission also underpins safety on site.
Start today
A problem shared is a problem halved. Don’t hesitate to get in touch to discuss your cladding needs.
Tim Kurniadi, General Manager – Remedial